Shift Patterns vs. Productivity: The Science Behind Workforce Scheduling
In UK manufacturing and production facilities, the constant hum of machinery doesn't always match the natural rhythms of the people operating them. As production demands continue to evolve in 2025, the way we structure work hours has profound implications not just for output metrics, but for the humans behind those metrics.
According to the UK Office for National Statistics, approximately 3.5 million workers in the UK regularly work shifts, with manufacturing and production industries representing a significant proportion of this figure. Yet despite this prevalence, many operations managers and production directors still rely on outdated scheduling approaches that prioritise machine uptime over human performance.
The consequences? Higher turnover rates (manufacturing experiences 15% higher turnover than the UK average according to Make UK's 2023 Labour Turnover Report), increased workplace accidents (37% higher in night shifts according to HSE data), and productivity plateaus that frustrate even the most experienced production managers.
Let's explore what the evidence actually tells us about shift patterns, their impact on your workforce, and how to design schedules that serve both business objectives and employee wellbeing.
The Biological Reality of Shift Work
Before discussing scheduling strategies, we must acknowledge the fundamental biological challenge: humans evolved to be active during daylight hours and rest at night. The circadian rhythm—our internal 24-hour clock—regulates everything from body temperature and hormone production to alertness and cognitive function.
Research from the University of Manchester's Centre for Biological Timing found that consistent disruption to this natural rhythm carries significant physiological consequences. These include:
- Impaired cognitive processing: A study published in the BMJ found reaction times slow by up to 50% during night shifts
- Decreased ability to focus: According to HSE research, attention spans shorten by approximately 30% during night work
- Compromised decision-making: The Sleep Research Centre at the University of Surrey reports error rates increase by 18-30% during night hours
- Suppressed immune function: Data from the Office for National Statistics shows shift workers report 60% more sick days annually
Dr. Timothy Morris, Chronobiologist at the University of Leeds, explains in a recent interview with The Manufacturer: "When we force the body to be active during its biological night, we're essentially asking it to perform in a state of physiological conflict. The body continues producing melatonin, the sleep hormone, while simultaneously trying to maintain alertness—creating a constant internal struggle."
This biological reality creates the foundational challenge for shift pattern design. However, understanding these constraints allows production managers to work within them rather than against them.
Common Shift Patterns: Comparing the Impact
Let's evaluate the most prevalent shift patterns in UK manufacturing and production environments:
1. Traditional Fixed Shifts (Early, Late, Night)
Productivity Impact: Makes consistent performance easier within teams but creates "weak points" during shift handovers. According to data from the Advanced Manufacturing Research Centre in Sheffield, fixed shifts see approximately 11% production loss during transition periods.
Worker Impact: Provides stability and routine, though those permanently assigned to nights face ongoing health challenges. Research from the British Medical Journal found that workers on permanent night shifts report 43% higher rates of sleep disorders than day workers.
2. Continental Shift Patterns (Rotating 3-4 Teams)
Productivity Impact: Maximises facility utilisation with continuous coverage, though productivity fluctuates as workers adapt to changing shifts. Manufacturing Excellence UK's 2023 report indicates productivity drops of 16-22% during the first 48 hours after a rotation.
Worker Impact: The rapid rotation between morning, afternoon, and night shifts creates significant physiological stress. A study from Loughborough University tracking UK factory workers found that cortisol levels (a stress hormone) remained elevated by 38% even on rest days for those working continental shifts.
3. Four On, Four Off (12-Hour Shifts)
Productivity Impact: Reduces handovers and provides consistent staffing for longer periods. The Manufacturing Technology Centre reports 13% fewer quality errors with this pattern compared to 8-hour shifts with more frequent handovers.
Worker Impact: Creates longer recovery periods but demands sustained concentration during extended shifts. HSE data shows that accident rates increase by 27% after the 9th hour of 12-hour shifts, particularly in physically demanding roles.
4. Flexitime with Core Hours
Productivity Impact: Less common in production environments but gaining traction in semi-automated facilities. Early adopters report productivity increases of 7-11% according to Make UK's 2023 Productivity Report, attributed primarily to improved worker satisfaction and reduced absenteeism.
Worker Impact: Offers greater work-life balance and accommodation of personal preferences. A study by Cranfield University's School of Management found retention rates improved by 34% when some degree of schedule flexibility was introduced in manufacturing settings.
Data-Driven Solutions: The New Approach to Shift Design
The most effective scheduling strategies now employ evidence-based approaches rather than simply perpetuating traditional patterns. Here's how leading manufacturers are rethinking their approach:
1. Chronotype-Informed Scheduling
Recent research from the University of Birmingham's Centre for Human Brain Health reveals that individuals have natural preferences for morning or evening activity (known as chronotypes). Their study published in Sleep Medicine found that aligning shift assignments with natural chronotypes improved productivity by 15-19% and reduced error rates by nearly a quarter.
Implementation strategy:
- Conduct chronotype assessments during recruitment and onboarding
- Allow employees to express shift preferences where possible
- Create teams with compatible chronotypes for specific shifts
- Offer premiums for working against natural preference when necessary
2. Circadian-Friendly Rotation Cycles
If rotation is unavoidable, the direction and speed matter significantly. The Institute for Manufacturing at Cambridge University found that forward-rotating shifts (morning → afternoon → night) allow for easier biological adaptation than backward rotation.
Furthermore, their research published in the International Journal of Industrial Ergonomics indicates that slower rotations (changing weekly rather than daily or every few days) reduce physiological stress markers by up to 27% compared to rapid rotation cycles.
3. Strategic Rest Periods and Shift Lengths
The relationship between shift length and productivity follows a clear pattern. Analysis from the Advanced Manufacturing Research Centre shows that:
- 8-hour shifts maintain consistent productivity throughout
- 10-hour shifts show a 7% decline in the final hour
- 12-hour shifts demonstrate a 19-26% decline in the final two hours
However, this relationship changes when adequate mid-shift breaks are incorporated. Manufacturers implementing structured rest protocols (including one 30-minute and two 15-minute breaks during 12-hour shifts) reported sustained productivity levels and a 23% reduction in quality errors according to the Work Foundation's 2023 report on shift work.
4. Environmental Modifications
Physical environment plays a crucial role in mitigating the negative impacts of shift work. A comprehensive study of UK production facilities by the Manufacturing Technology Centre found significant performance improvements with these interventions:
- Dynamic lighting systems that adjust colour temperature throughout shifts (mimicking natural daylight cycles) improved alertness by 24% during night shifts
- Temperature regulation (slightly cooler environments during night shifts) reduced reported fatigue by 18%
- Acoustic modifications to reduce unnecessary background noise decreased stress markers by 11%
5. Nutrition and Hydration Support
The University of Surrey's Sleep Research Centre found that shift workers frequently develop poor dietary habits due to disrupted eating schedules and limited food options. Their research published in Chronobiology International shows that providing nutrition education and healthy food options during shifts improved cognitive performance by 13-17% compared to control groups.
Forward-thinking manufacturers now provide:
- 24-hour access to nutritious meals and snacks
- Hydration stations throughout production areas
- Guidance on strategic caffeine consumption
- Pre-prepared meal options for take-home
Case Study: Revolution at West Midlands Engineering Firm
The Engineer magazine profiled a West Midlands precision engineering firm that implemented a comprehensive shift pattern redesign in 2023 after experiencing 32% annual turnover and stagnating productivity metrics. As documented in Make UK's Manufacturing Success Stories, their approach included:
- Employee chronotype assessment and preference mapping
- Introduction of self-selecting teams for specific shift patterns
- Forward-rotating schedules with minimum 48-hour adaptation periods
- Environmental modifications including dynamic lighting and acoustic improvements
- Structured break protocols with nutrition support
The results after 18 months, as verified by EEF Productivity Benchmarking:
- Productivity increased by 22%
- Turnover reduced to 14%
- Absenteeism decreased by 31%
- Workplace incidents reduced by 47%
- Employee satisfaction scores improved by 37%
As reported in The Manufacturer, the operations director reflected: "We'd spent years treating our machinery better than our people—ensuring optimal operating conditions for equipment while expecting humans to simply adapt. Reversing this thinking has transformed our business."
Implementing Change: Practical Considerations
Transitioning to new shift patterns requires careful planning to avoid disruption. Industry experts recommend these implementation steps:
1. Data Gathering and Analysis
Before making changes, collect baseline performance metrics:
- Productivity by shift and time period
- Error/quality incidents by hour and shift
- Absenteeism patterns
- Employee turnover by shift
- Self-reported fatigue and satisfaction scores
These metrics provide both justification for change and benchmarks for measuring success, according to the Institution of Occupational Safety and Health.
2. Employee Consultation
Employee involvement isn't just good practice—it's essential for successful implementation. Make UK's Change Management Guide shows that shift pattern changes implemented with meaningful employee consultation are 3.4 times more likely to succeed than those imposed unilaterally.
Consultation should include:
- Clear explanation of the business rationale
- Opportunities for feedback and alternative suggestions
- Transparent discussion of potential impacts
- Consideration of personal circumstances
3. Phased Implementation
Radical overnight changes typically create resistance and disruption. The Manufacturing Advisory Service recommends a phased approach:
- Pilot new patterns with volunteer teams
- Run parallel systems during transition periods
- Implement fully after demonstrating success
4. Continuous Monitoring and Adjustment
No shift pattern is universally perfect. The Institute of Employment Studies recommends successful implementations include:
- Regular review of key performance metrics
- Feedback mechanisms for reporting issues
- Willingness to make adjustments based on data
- Ongoing communication about outcomes
The Future of Shift Pattern Design
As we look ahead, several emerging trends will likely shape shift pattern design in UK manufacturing:
1. AI-Driven Scheduling
Artificial intelligence is beginning to transform scheduling by analysing complex patterns of productivity, absence, and performance. Research from the University of Warwick's Manufacturing Group shows systems using machine learning can identify optimal shift patterns based on historical data and can even predict which employees will perform best in specific slots.
2. Hybrid Production Models
Some manufacturers are exploring hybrid models where critical processes run 24/7 while supporting functions operate on more limited schedules. The Work Foundation reports this targeted approach concentrates shift work where it delivers maximum value while reducing its overall footprint.
3. Compressed Working Time
The four-day working week trials in the UK, documented by Autonomy UK have yielded interesting insights for manufacturing. While continuous production necessitates shift coverage, some facilities are experimenting with compressed schedules (four 10-hour shifts instead of five 8-hour shifts) to improve work-life balance without reducing operating hours.
Conclusion
As we look ahead, several emerging trends will likely shape shift pattern design in UK manufacturing:
1. AI-Driven Scheduling
Artificial intelligence is beginning to transform scheduling by analysing complex patterns of productivity, absence, and performance. Research from the University of Warwick's Manufacturing Group shows systems using machine learning can identify optimal shift patterns based on historical data and can even predict which employees will perform best in specific slots.
2. Hybrid Production Models
Some manufacturers are exploring hybrid models where critical processes run 24/7 while supporting functions operate on more limited schedules. The Work Foundation reports this targeted approach concentrates shift work where it delivers maximum value while reducing its overall footprint.
3. Compressed Working Time
The four-day working week trials in the UK, documented by Autonomy UK have yielded interesting insights for manufacturing. While continuous production necessitates shift coverage, some facilities are experimenting with compressed schedules (four 10-hour shifts instead of five 8-hour shifts) to improve work-life balance without reducing operating hours.
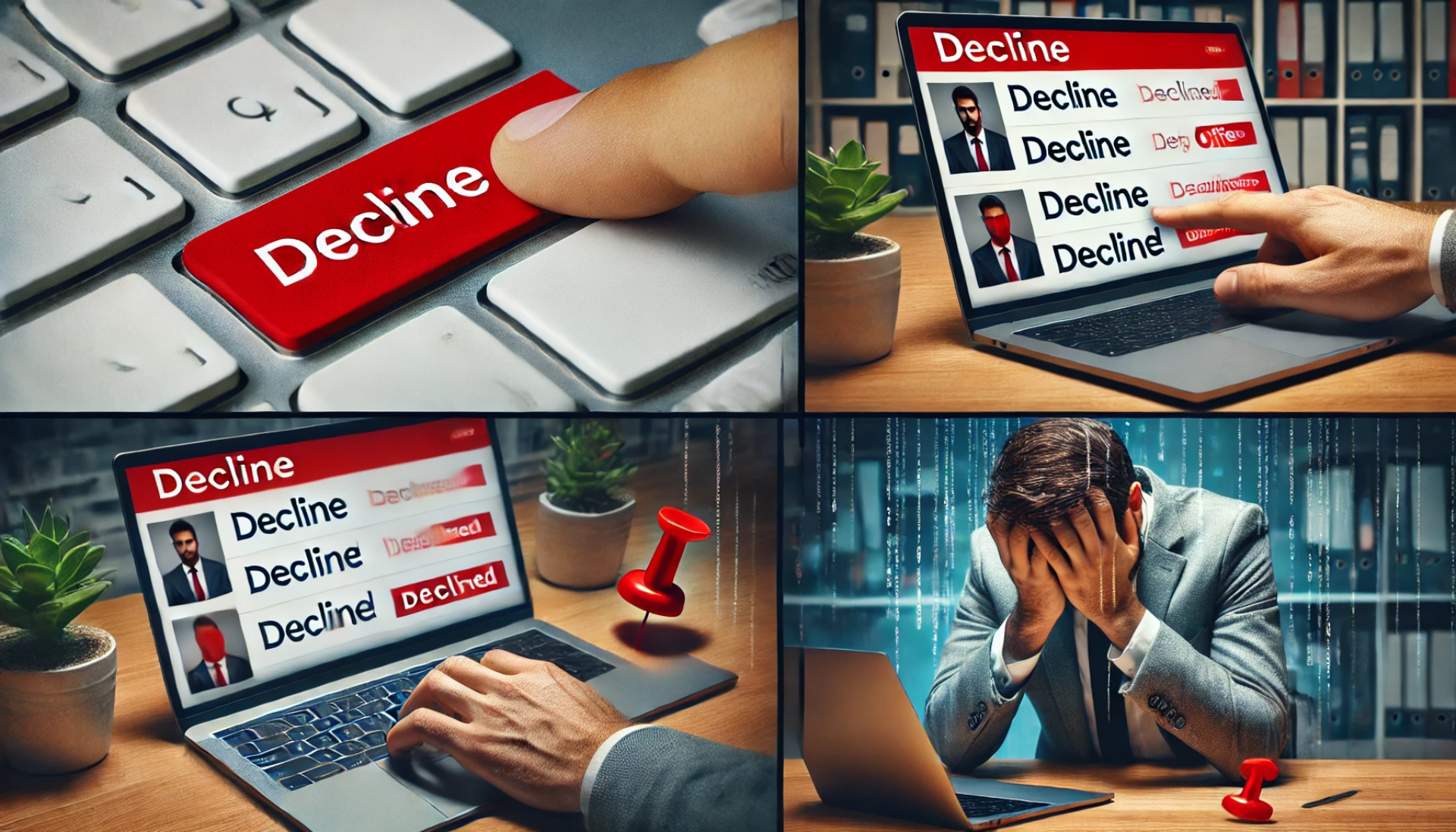
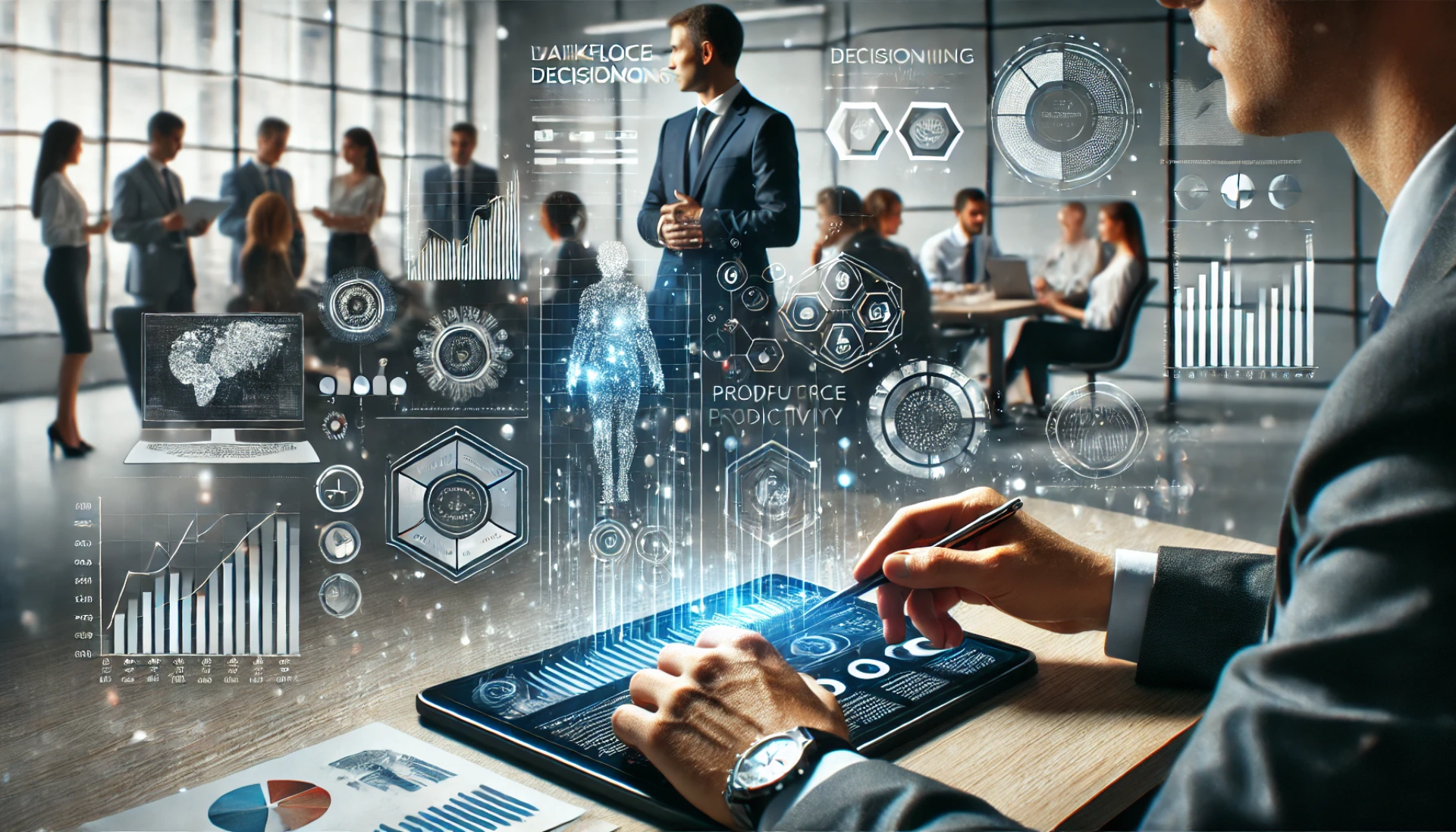
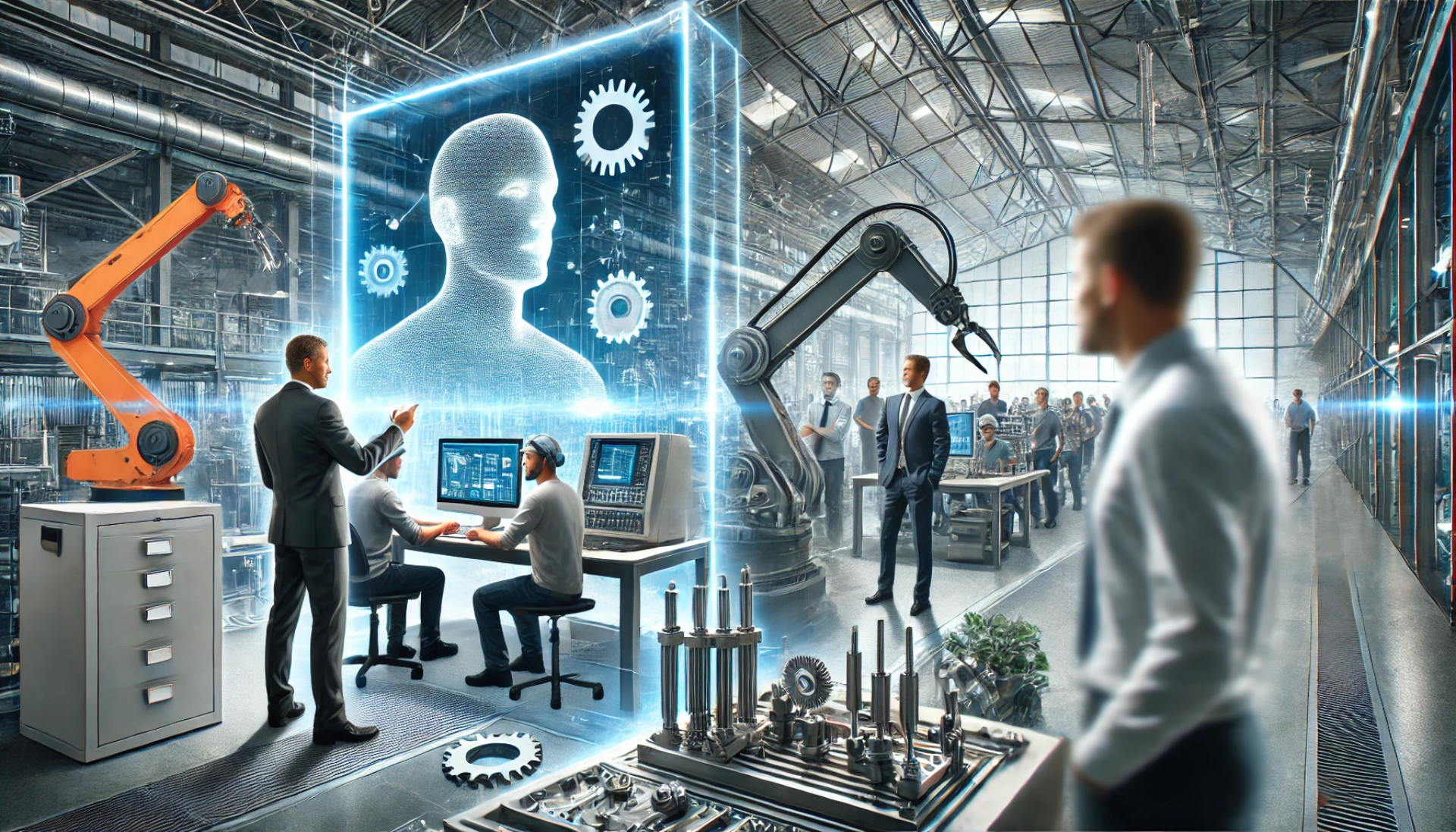
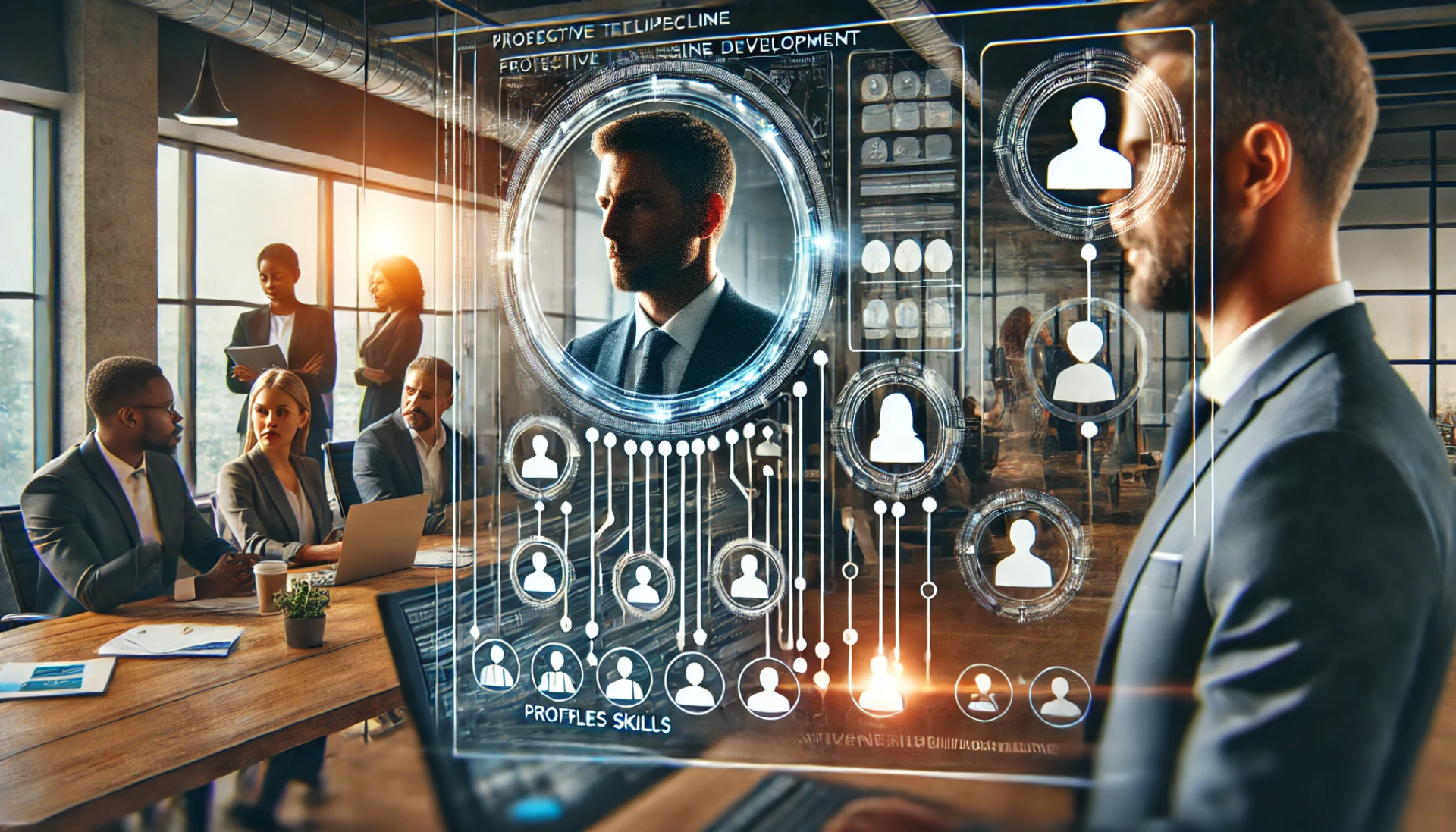
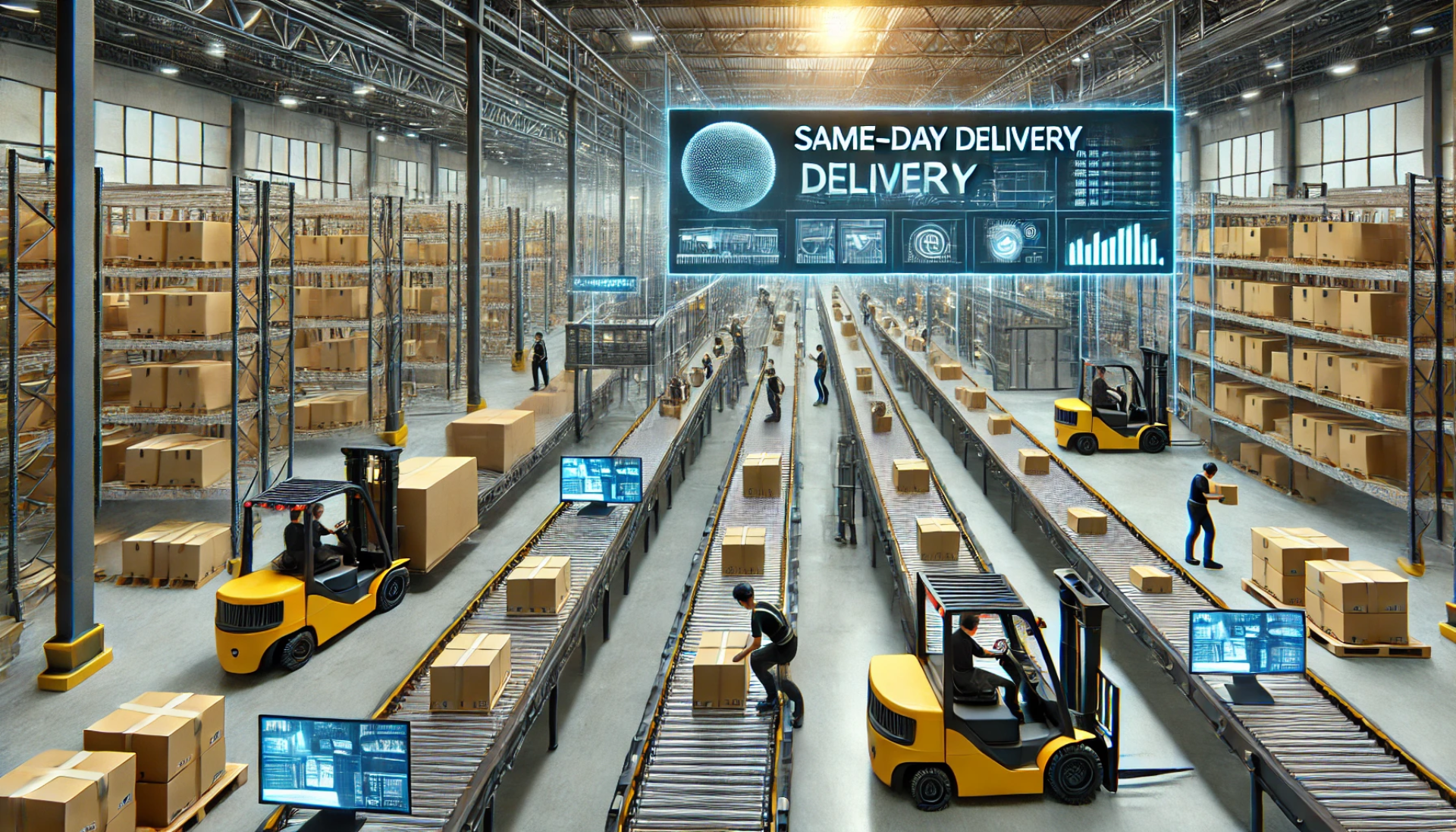
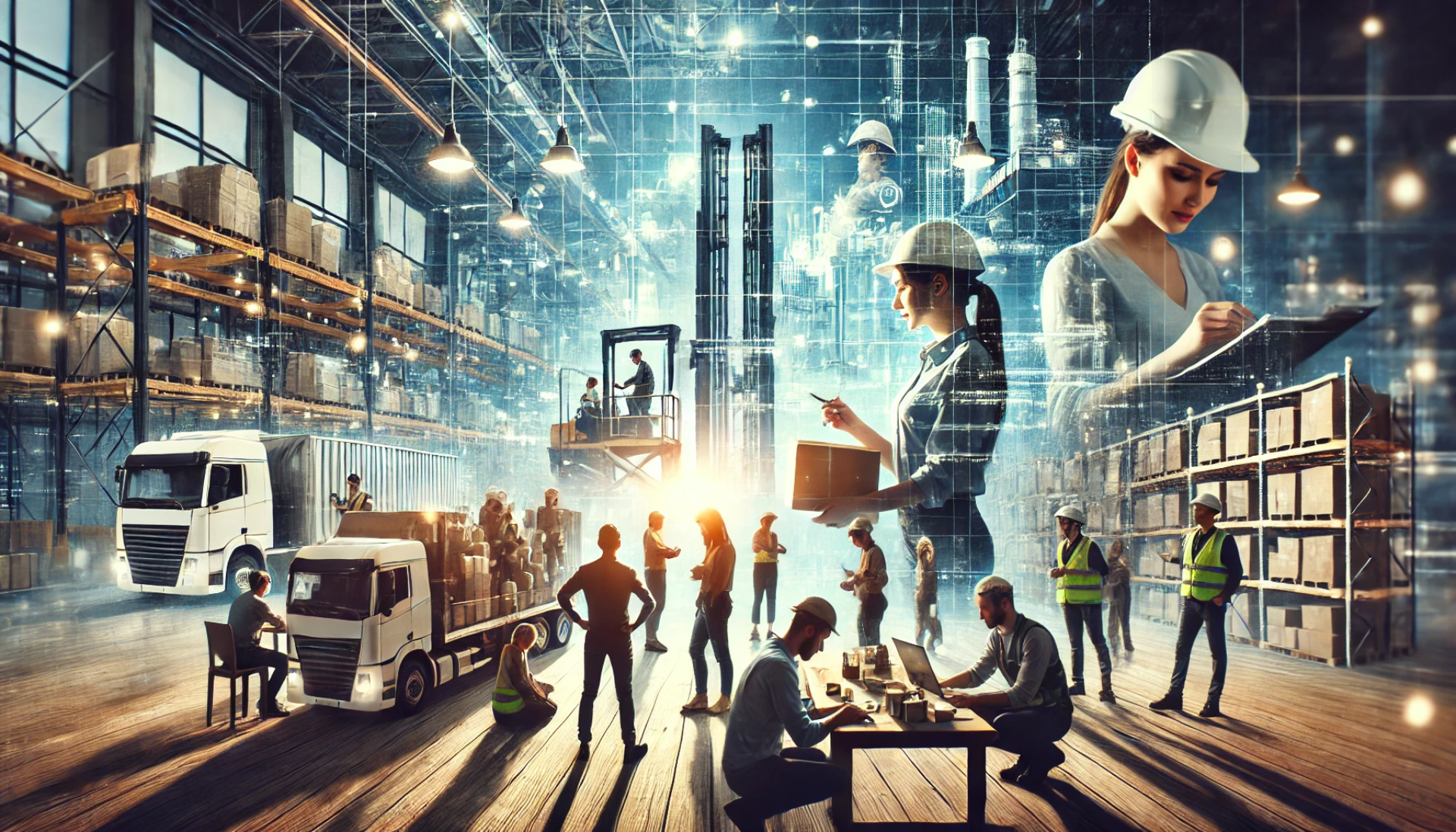
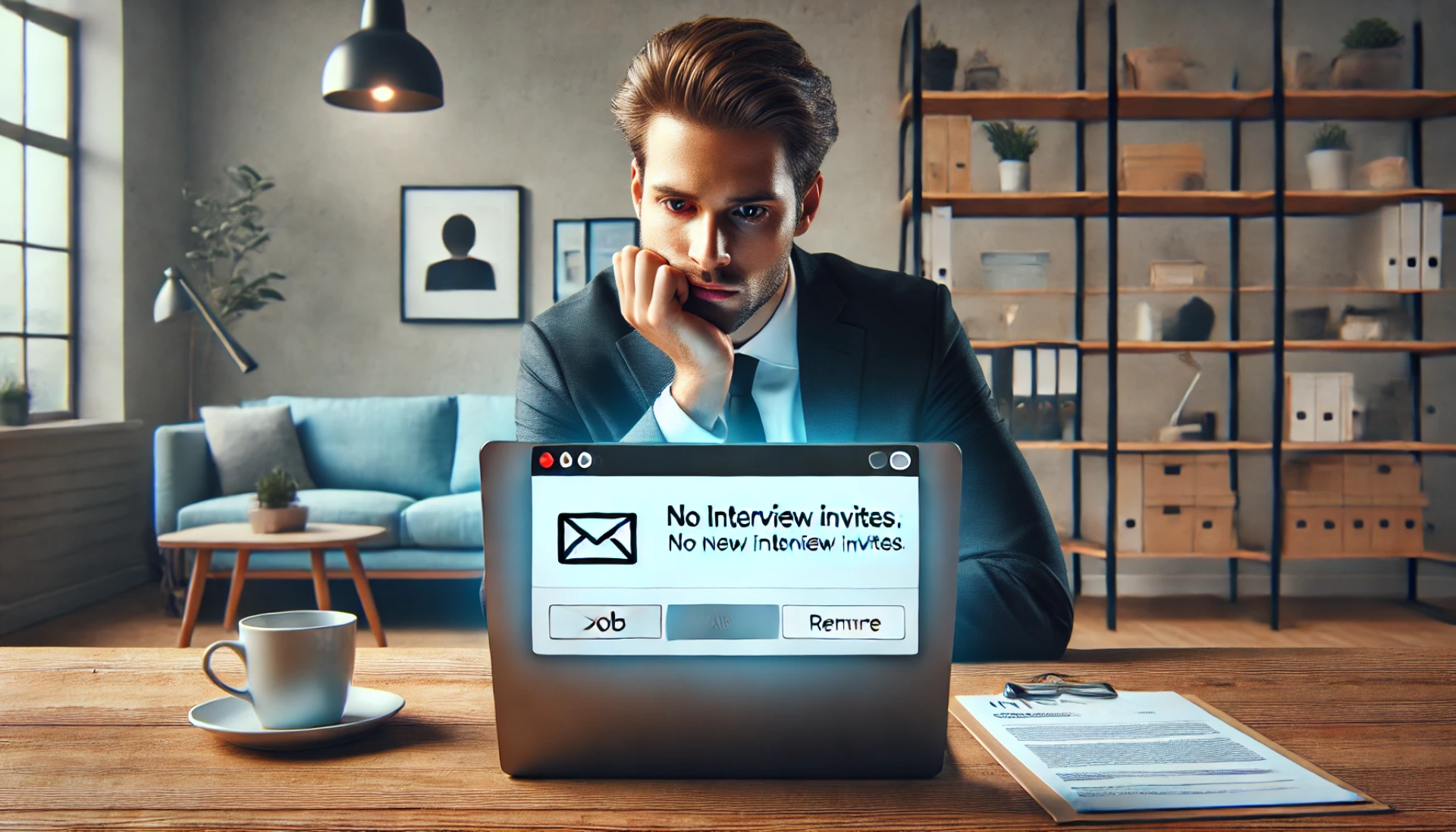
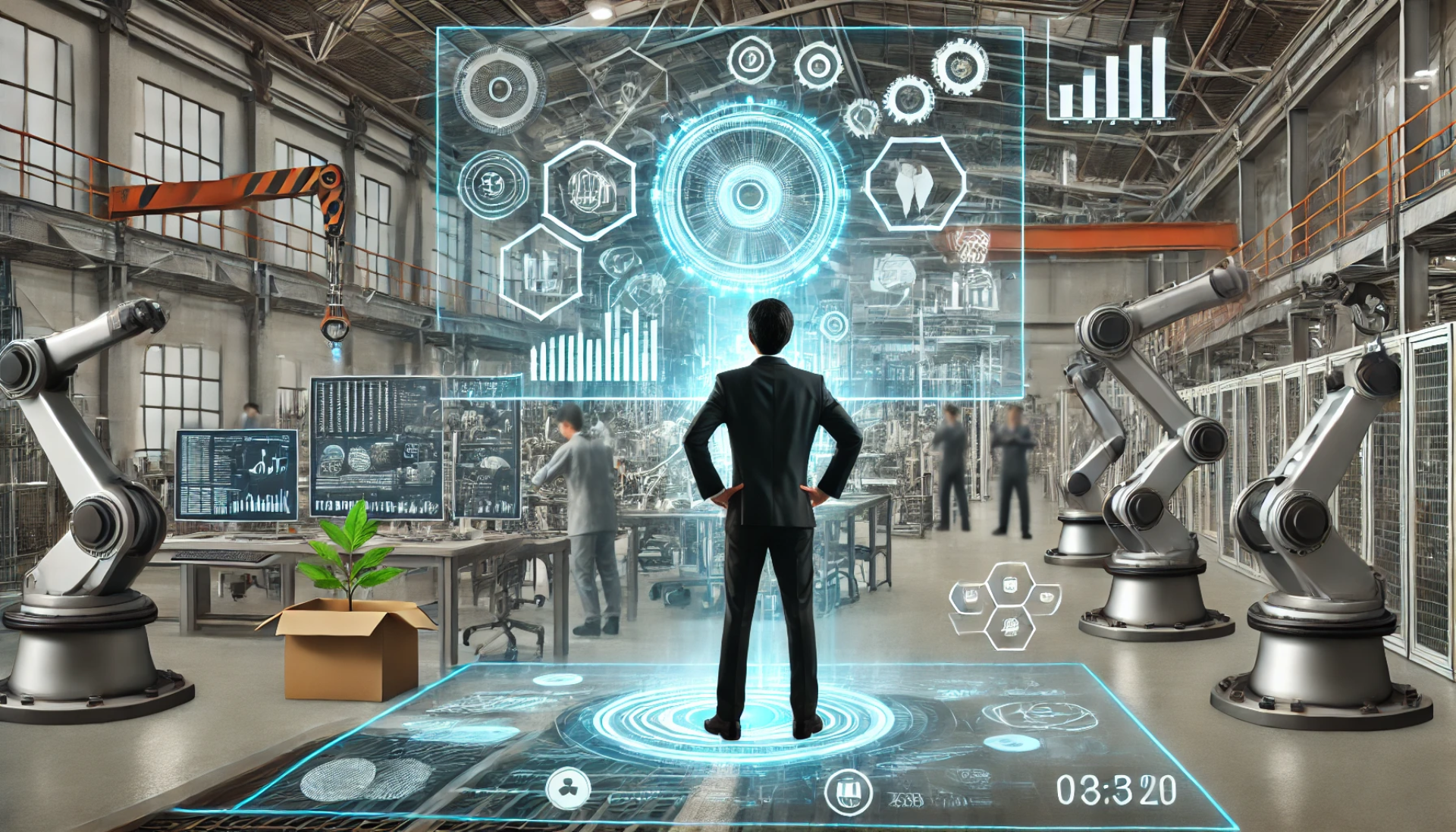
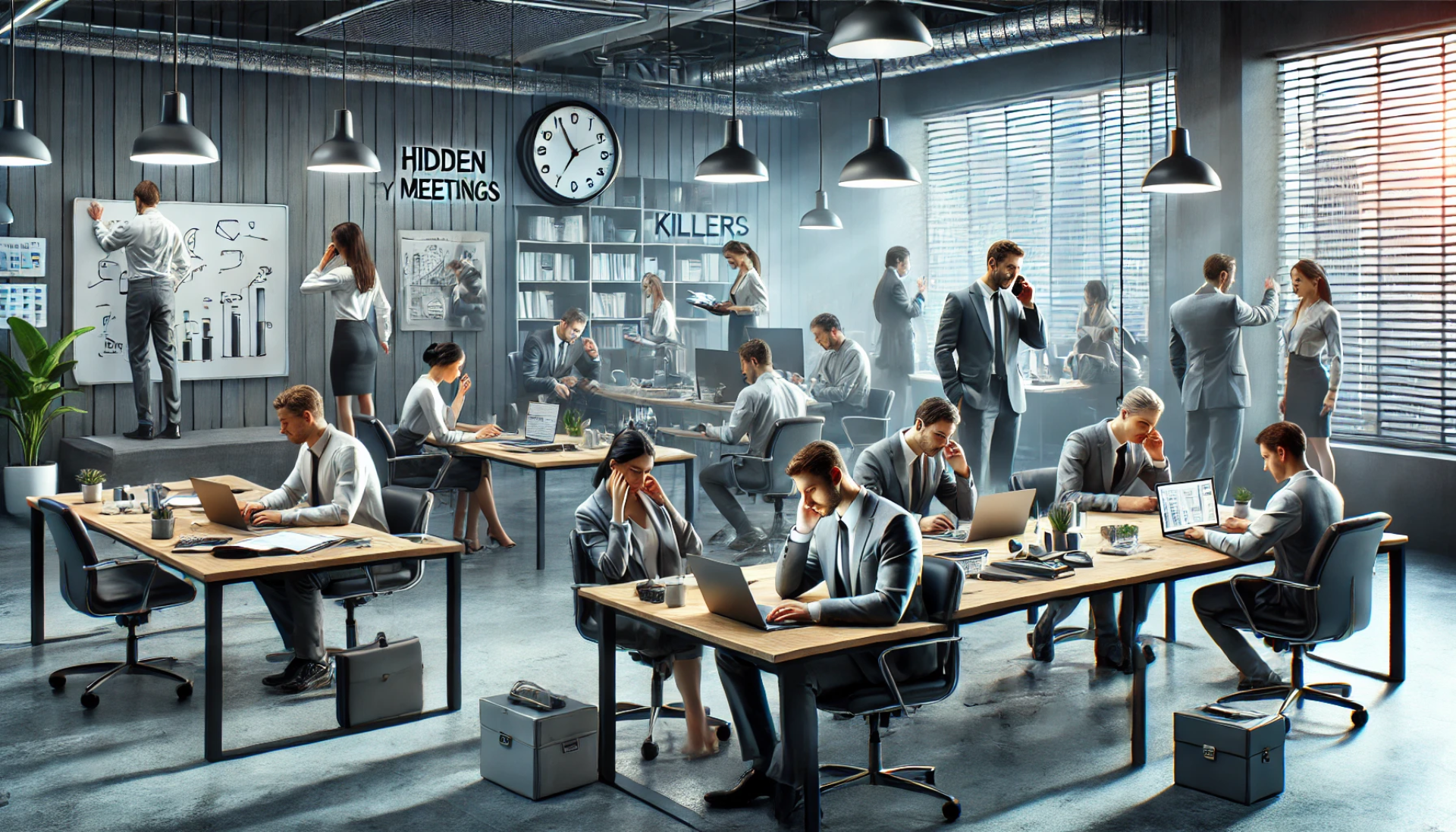
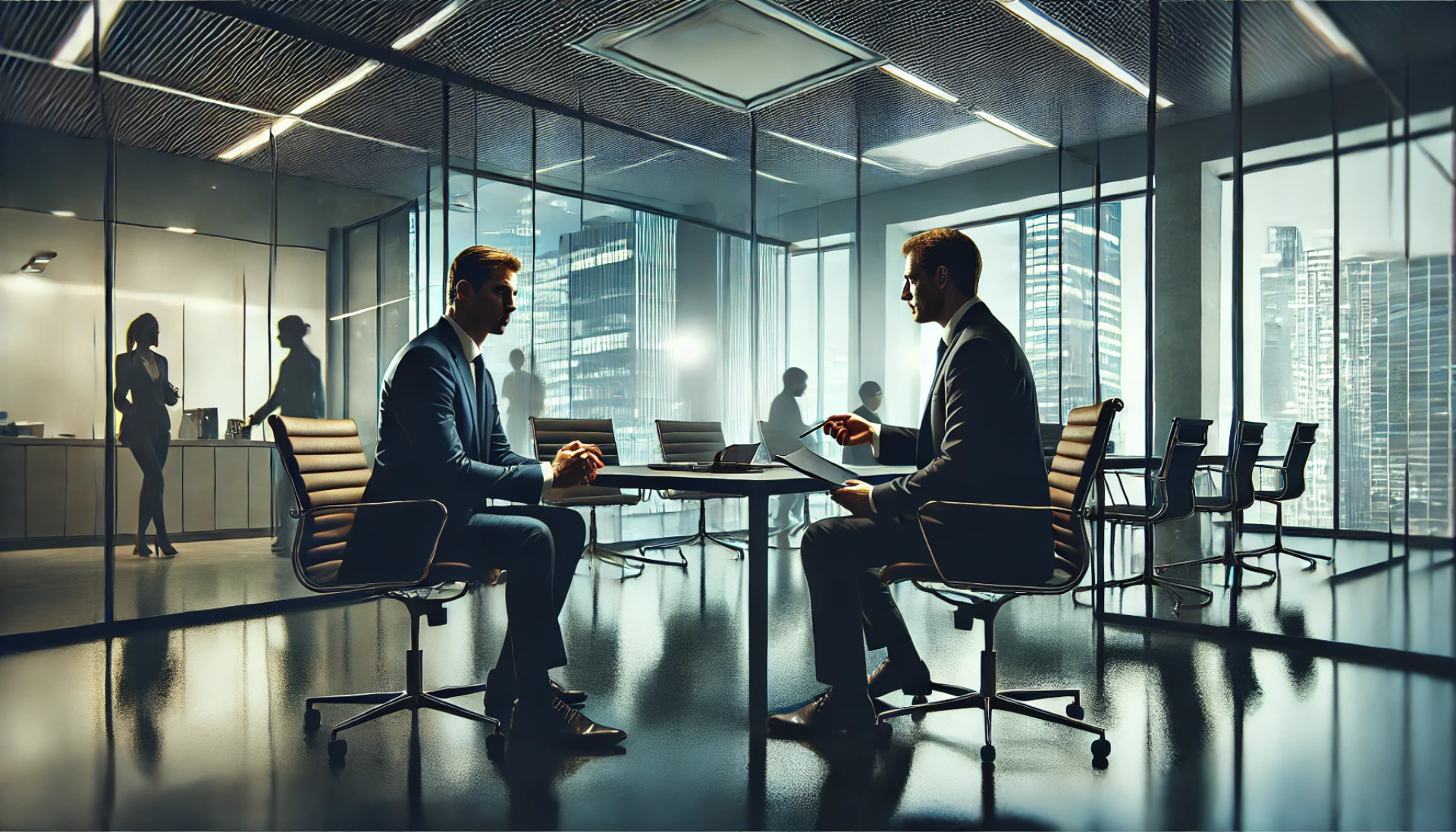