How to Build a High-Performance Warehouse Team Without Increasing Your Labour Costs
In today’s fast-paced logistics environment, building a high-performance warehouse team isn’t about adding more staff—it’s about working smarter with the people you already have. By optimising team structures, streamlining workflows, and implementing targeted recruitment and training strategies, you can boost productivity while keeping labour costs in check. This post delves into granular, actionable tactics and real-world case examples to help you create an efficient, agile warehouse operation.
Optimising Team Structures
- Cross-Skilling: Equip your team members with multiple skills so they can move seamlessly between roles during peak periods. For example, training pickers in basic inventory management or forklift operation not only reduces downtime but also allows you to adapt quickly to sudden workflow changes.
- Clear Role Definitions: Document specific responsibilities for every role. Detailed job briefs help reduce duplication of effort and ensure that each team member understands how their work contributes to overall efficiency.
- Empower Frontline Leaders: Appoint experienced team leads who can oversee operations on the warehouse floor. Empower them with decision-making authority to address bottlenecks immediately, fostering a sense of ownership that translates into better performance.
Enhancing Workflow Efficiency
- Detailed Process Mapping: Break down every step of your warehouse operations—from receiving and storage to order picking and shipping. Identify redundant or unnecessary steps that can be eliminated or automated.
- Implement Lean Practices: Use lean management techniques to streamline processes. This might include 5S (Sort, Set in order, Shine, Standardise, Sustain) methodologies, which help maintain an organised work environment and reduce wasted motion.
- Leverage Technology:
- Warehouse Management Systems (WMS): A robust WMS provides real-time data, helping you monitor productivity and adjust processes quickly.
- Automation Tools: Technologies like conveyor systems, automated sorters, or even wearable devices can reduce manual errors and speed up order fulfillment.
- Mobile Technology: Equip staff with handheld devices to track inventory and update order statuses on the fly, further reducing downtime between tasks.
Optimising Physical Layout
- Strategic Storage: Organise your warehouse so that high-turnover items are easily accessible. A well-planned layout minimises travel time and reduces fatigue.
- Dynamic Slotting: Regularly review and adjust item locations based on seasonal trends or changes in demand. This ensures that the most frequently picked items are always within reach.
Smart Recruitment and Training
- Targeted Hiring: Look beyond traditional warehouse roles. Candidates with a background in process optimisation or a keen interest in technology can bring innovative ideas to your team. Consider hiring for potential rather than just immediate technical skills.
- Cultural Fit: During the recruitment process, assess candidates not only for technical ability but also for adaptability, teamwork, and a proactive mindset. These qualities are critical for a dynamic warehouse environment.
Training and Development
- Comprehensive Onboarding: Develop a robust onboarding programme that familiarises new hires with your processes, technology, and company culture. Detailed training manuals, hands-on demonstrations, and mentoring can significantly reduce the learning curve.
- Continuous Learning:
- Regular Workshops: Schedule periodic training sessions on new technologies, safety procedures, and efficiency practices.
- Certifications: Encourage staff to pursue industry-recognised certifications in areas such as forklift operation, inventory management, or lean manufacturing.
- In-House Upskilling: Create an environment where employees can suggest process improvements and then train their peers on these innovations. This not only boosts efficiency but also empowers staff, leading to higher engagement and retention.
Real-World Success Stories
DHL Supply Chain Smart Glasses Pilot
DHL Supply Chain recently ran a pilot programme integrating smart glasses into their order picking process. The wearable technology provided real-time data and visual cues, which enabled pickers to locate items faster and with greater accuracy. The results were impressive: a 20% improvement in picking efficiency and a significant reduction in overtime, all achieved without increasing headcount. This case study illustrates how investing in technology and training can directly translate into labour cost savings while enhancing overall performance.
XPO Logistics Workforce Optimisation
XPO Logistics is another notable example. By reconfiguring team structures and implementing a comprehensive cross-training programme, they improved throughput by 15% while keeping labour costs stable. Their approach focused on empowering frontline supervisors and using data analytics to monitor performance, leading to smarter scheduling and more effective use of existing staff.
Implementing Granular Performance Metrics
Key Performance Indicators (KPIs)
- Order Accuracy: Track the number of picking errors and implement immediate feedback loops. Reducing errors can cut down on costly rework and returns.
- Throughput Time: Monitor the time taken from receiving an order to shipping it. A faster throughput time often correlates with a well-organised team and efficient processes.
- Labour Utilisation: Analyse overtime hours and idle time. Identifying peaks and troughs in labour usage helps in scheduling more effectively.
- Employee Engagement: Regular surveys and performance reviews can help gauge morale. Engaged employees are more productive and less likely to leave, which saves on recruitment and training costs.
Data-Driven Decision Making
- Real-Time Dashboards: Use software tools that provide instant insights into warehouse operations. Dashboards help supervisors identify issues before they escalate.
- Regular Audits: Conduct periodic reviews of workflow efficiency and employee performance. Use the insights to refine processes continuously.
Future-Proofing Your Warehouse
- Pilot New Technologies: Before fully investing, run pilot programmes to evaluate the return on investment. This approach minimizes risk and allows you to scale successful innovations gradually.
- Flexible Workforce Planning: Use data to forecast demand and adjust staffing levels accordingly. Temporary contracts, part-time roles, or on-call staff can offer flexibility without a long-term cost increase.
- Cultivating a Culture of Continuous Improvement: Encourage feedback and innovation at all levels. When employees feel they have a stake in the company’s success, they’re more likely to contribute ideas that lead to cost savings and performance improvements.
Final Thoughts
- Pilot New Technologies: Before fully investing, run pilot programmes to evaluate the return on investment. This approach minimizes risk and allows you to scale successful innovations gradually.
- Flexible Workforce Planning: Use data to forecast demand and adjust staffing levels accordingly. Temporary contracts, part-time roles, or on-call staff can offer flexibility without a long-term cost increase.
- Cultivating a Culture of Continuous Improvement: Encourage feedback and innovation at all levels. When employees feel they have a stake in the company’s success, they’re more likely to contribute ideas that lead to cost savings and performance improvements.
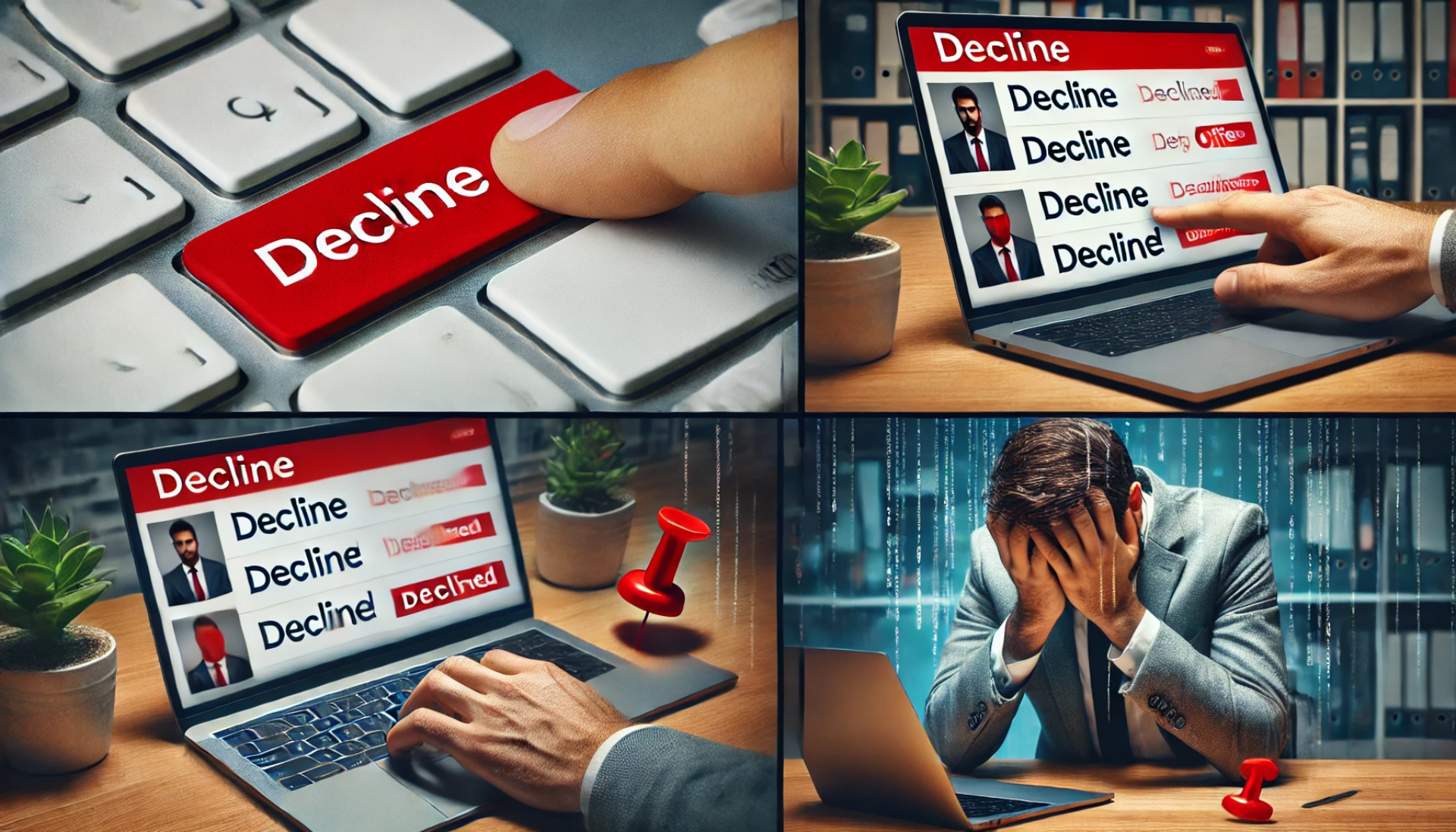
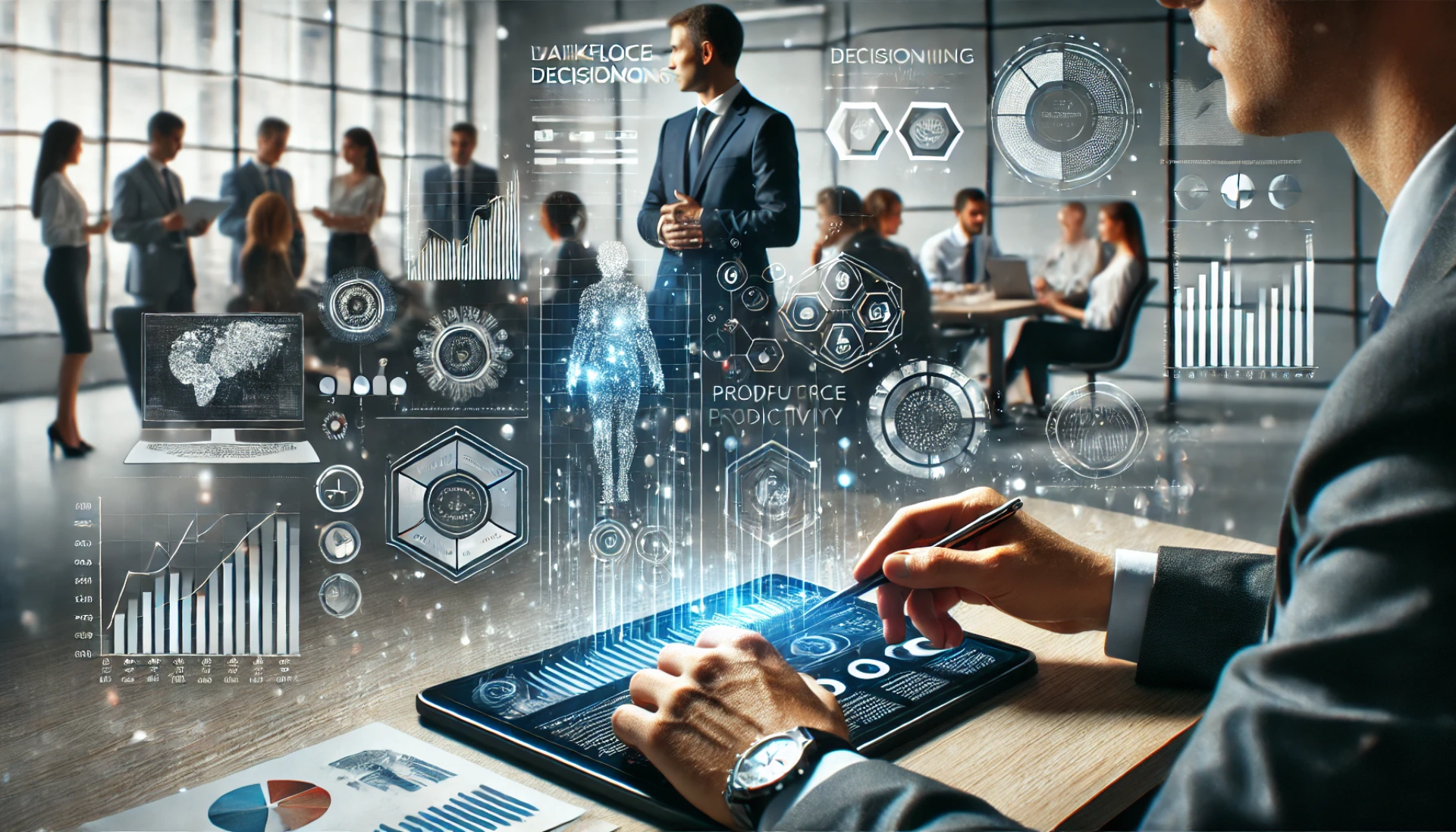
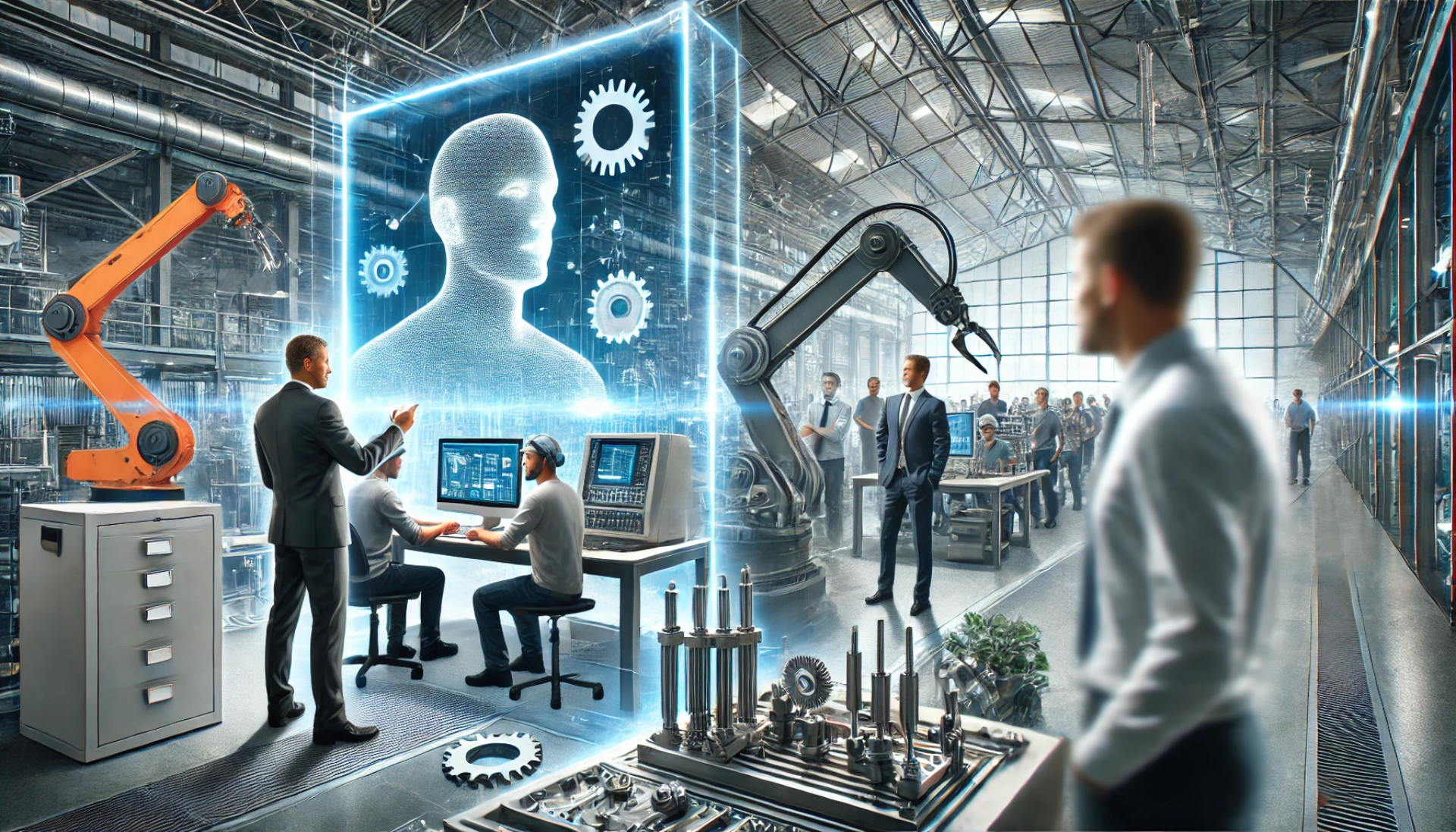
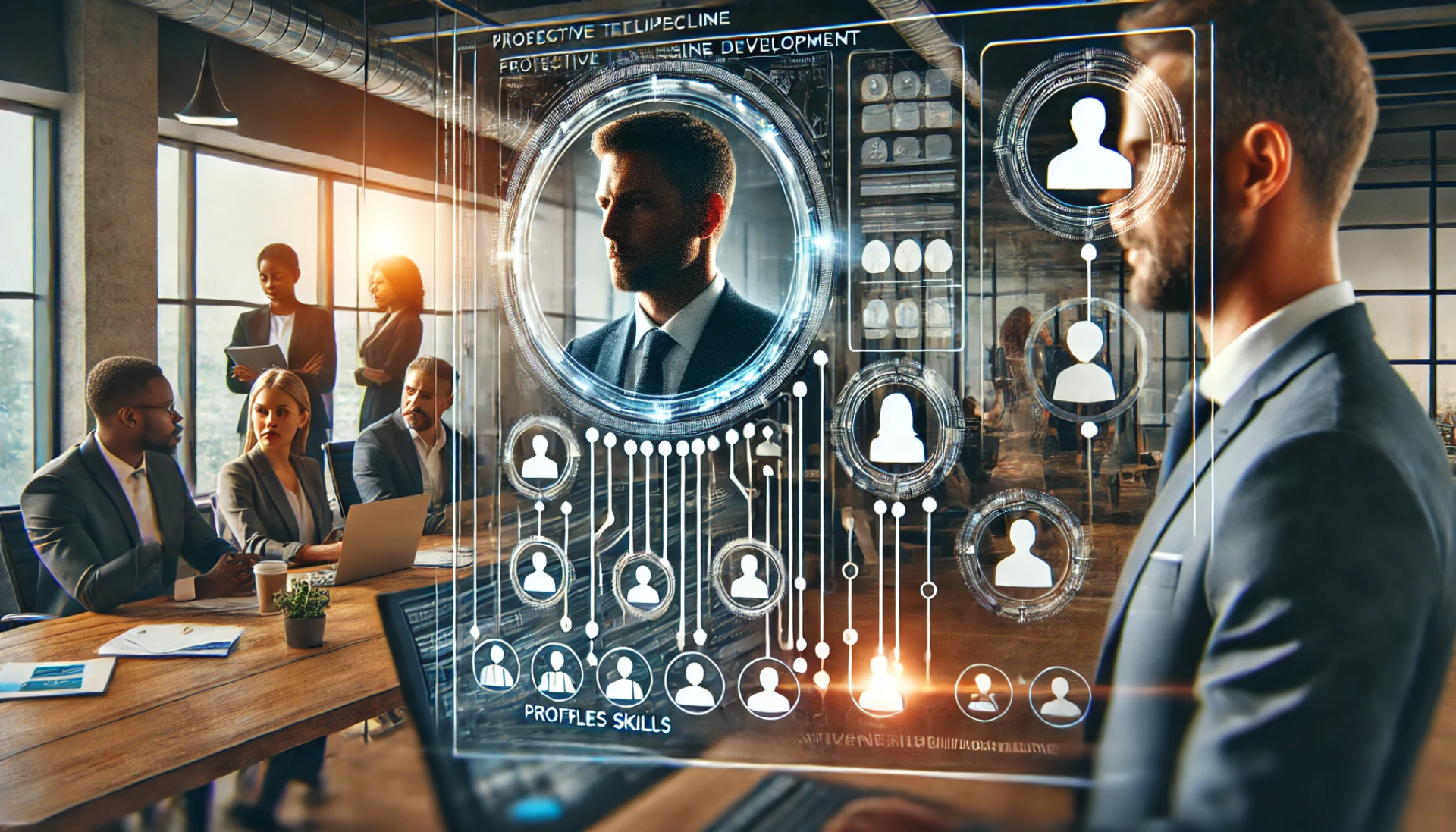
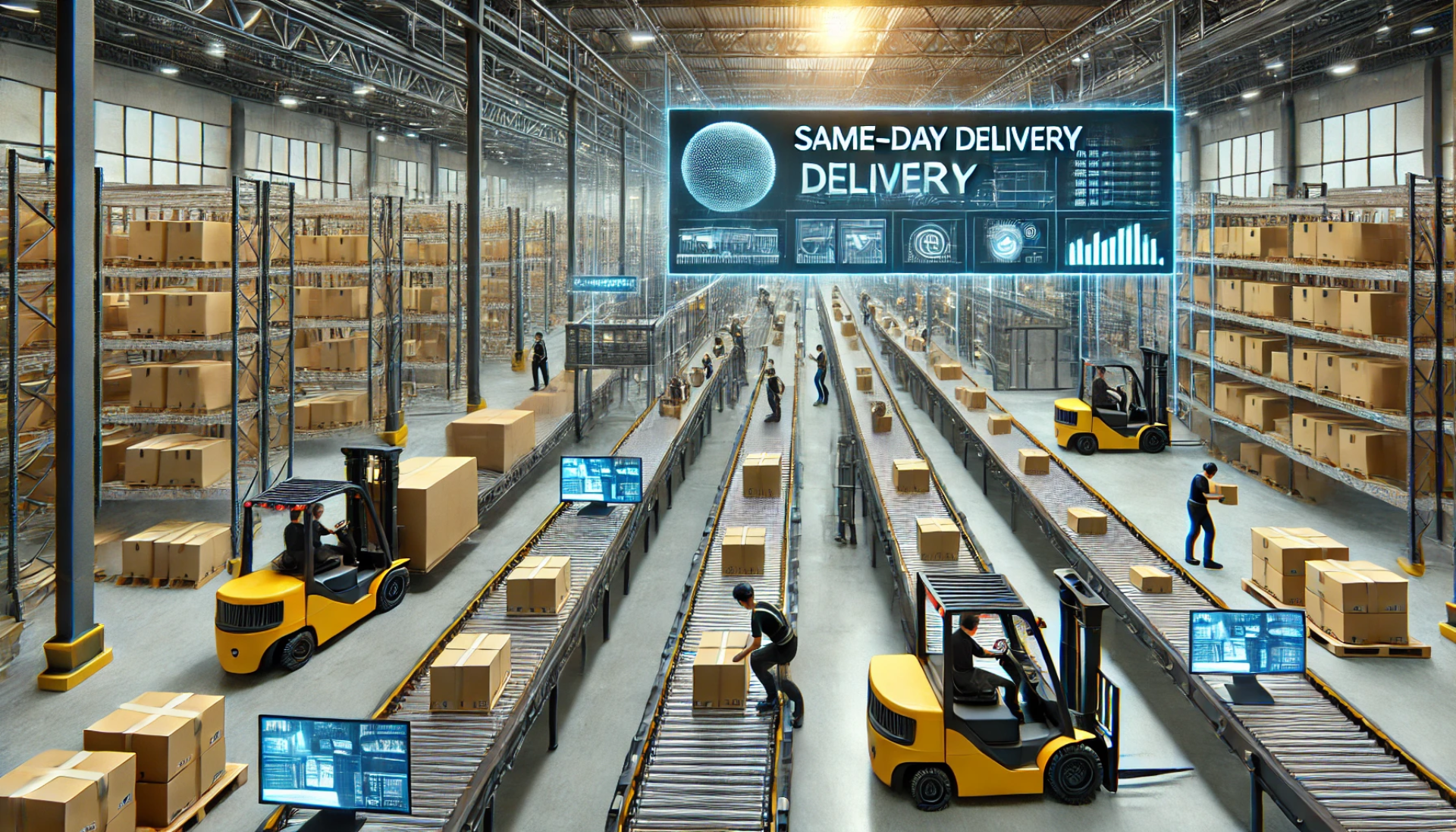
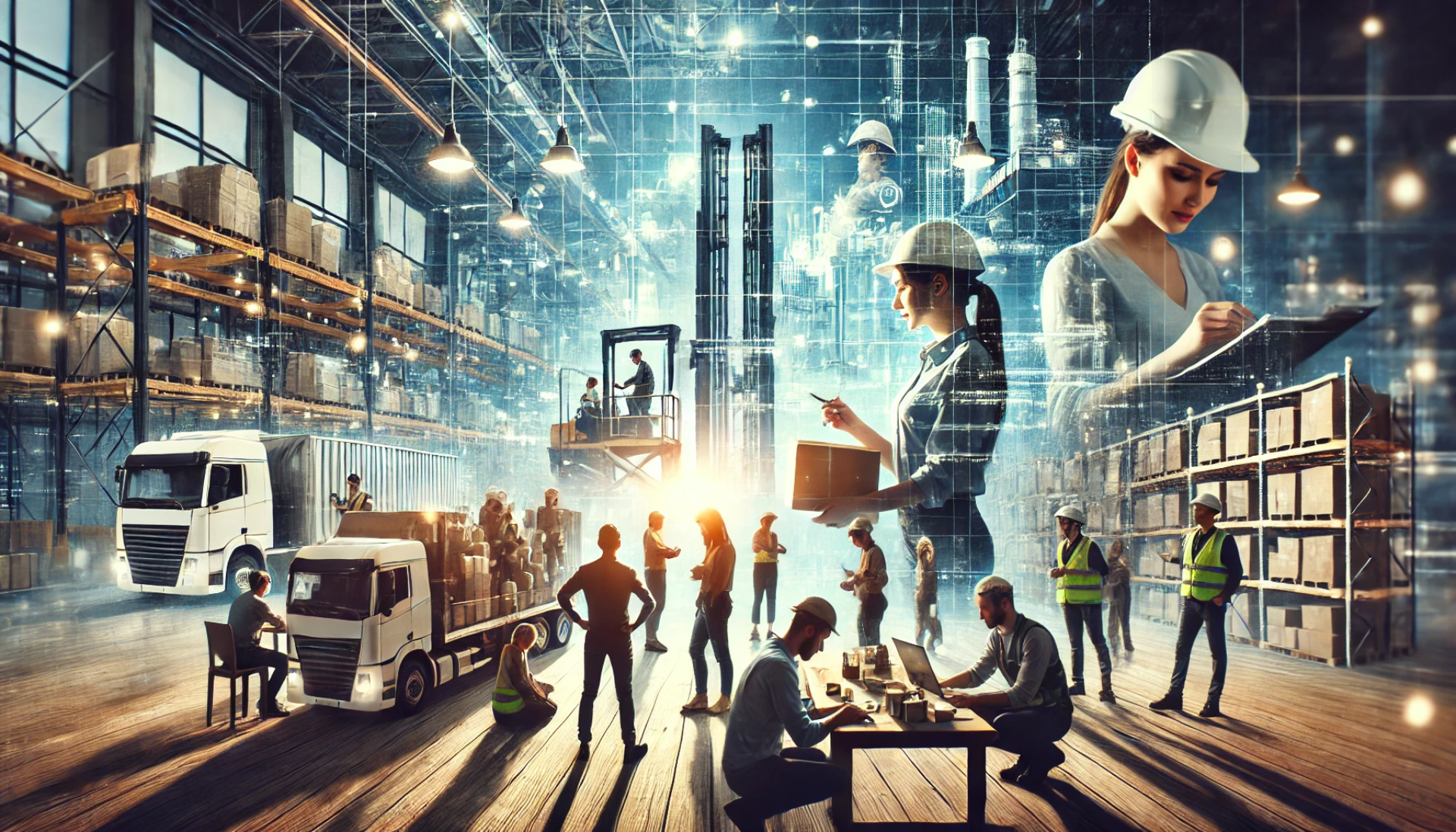
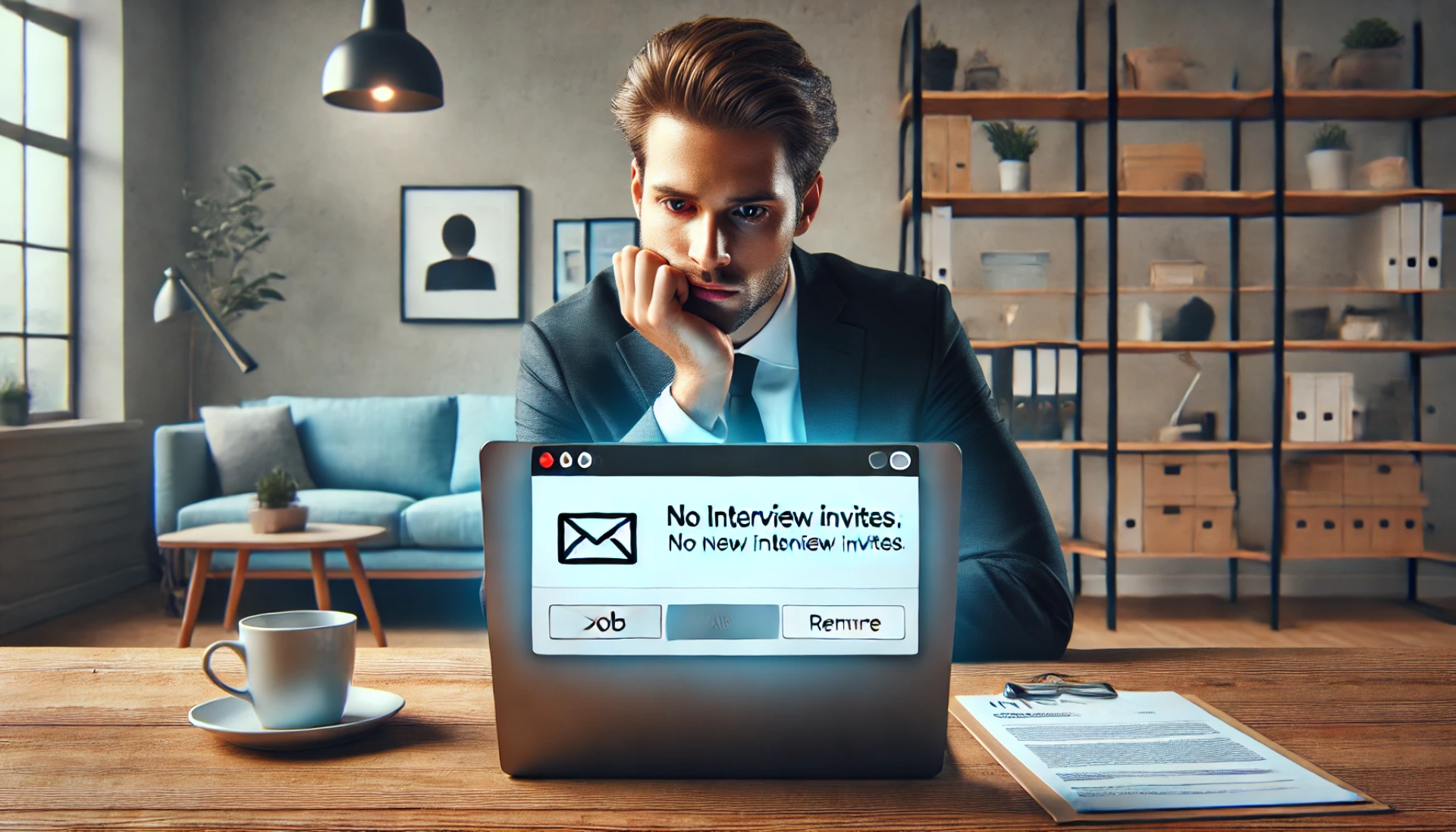
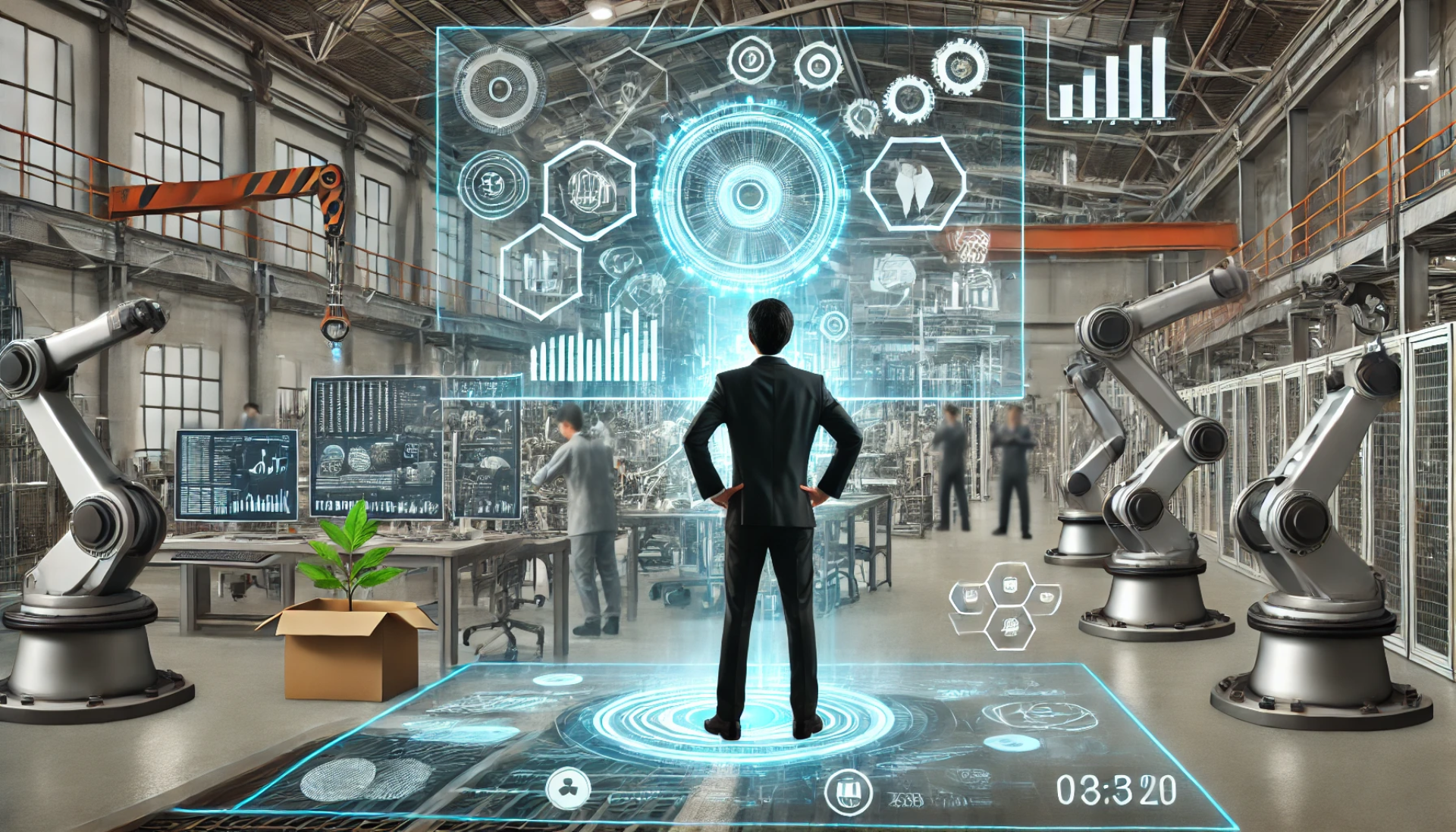
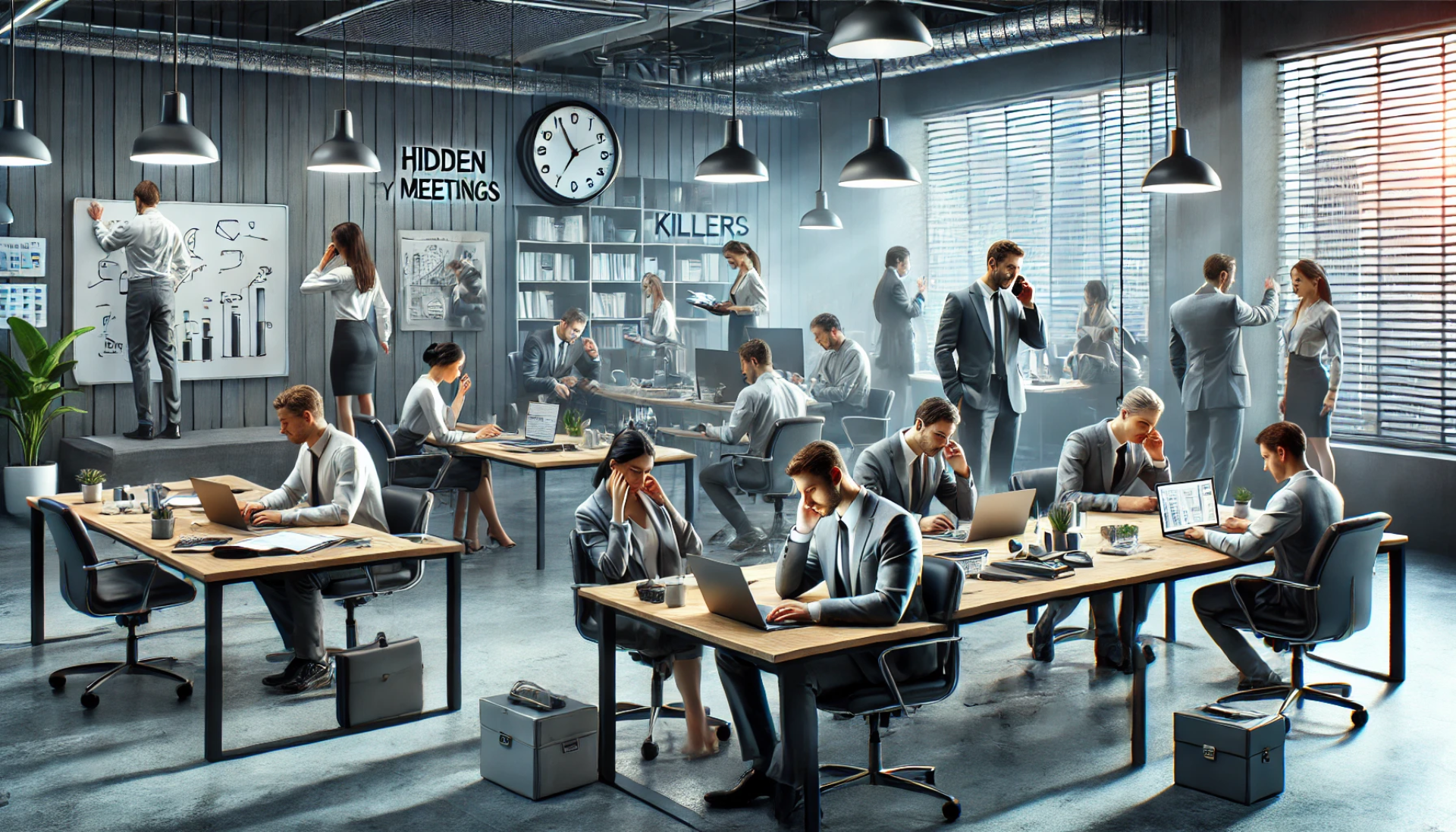
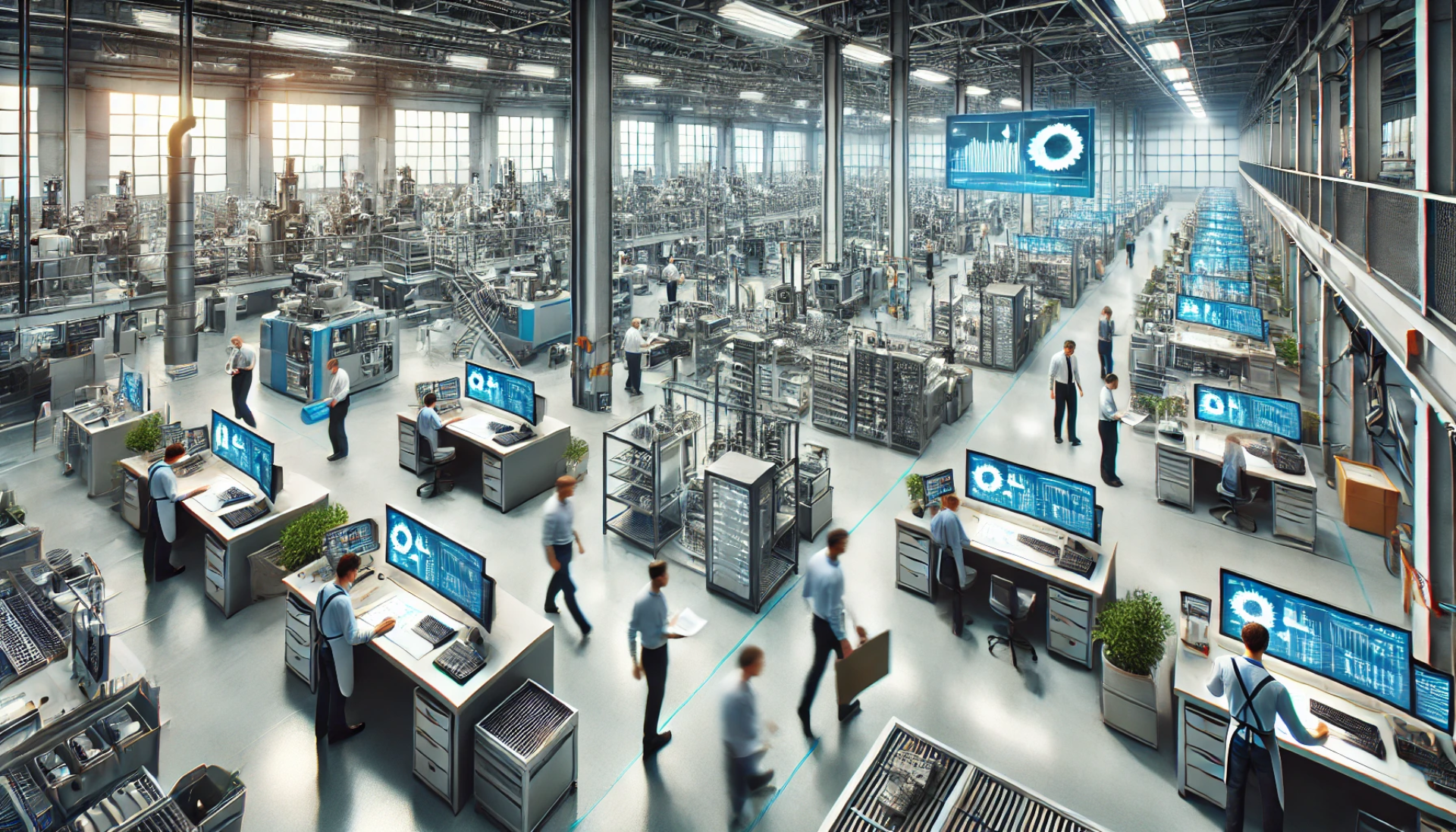